历经两代科研人20余年技术攻关,开发并集成出世界首创以煤为原料的“梯级变换制氢—铁串钌氨合成”合成氨成套技术。此举打破了国外20多年的技术垄断,将结束我国合成氨工业高能耗局面,有望撬动上千亿元产值提升空间。
记者从福州大学获悉,日前,“铁钌接力催化”氨合成成套技术开发及工业应用项目通过了由中国石油和化学工业联合会在京组织的科技成果鉴定。鉴定委员会一致认为:该成果总体达到国际先进水平,其中高性能钌基氨合成催化剂制备技术及以煤为原料的铁钌接力催化氨合成工艺处于国际领先水平。
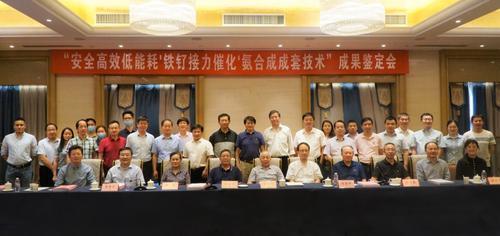
成果鉴定现场
氨是世界上最重要的化工原料之一。2019年我国氨产量5600多万吨,约占世界总产量的34%,年消耗高达8000多万吨标准煤,节能降耗增效压力巨大。为此,国家把发展高效低压合成氨大型化技术,列为突破制约化肥行业转型升级的重大关键技术之一。更为重要的是,氨也是无碳富氢载体,发展以氨为氢能载体是解决氢能储运和可再生能源电力利用的最可行途径之一。因此,大力发展合成氨工业,不仅是粮食安全和节能减排的重大需求,而且有助于贯通传统化工产业和新能源产业,为国家能源结构多元化提供一条重要新途径。
据介绍,该技术由福州大学、中国石油石油化工研究院、北京三聚环保、江苏禾友化工、南京聚拓化工和湖南安淳等单位共同研发,实现了多项关键技术突破:首创了高效制备石墨化碳载体新工艺技术、低钌载量的高性能钌基氨合成催化剂新技术和安全高效低能耗铁钌接力氨合成新工艺,建成了世界首套以煤为原料的铁钌接力催化氨合成工业装置并实现安全稳定长周期运行,形成了钌基氨合成催化剂生产—应用—回收成套工程化新技术。
据福州大学科技部“化肥催化”重点领域创新团队负责人介绍,利用该技术,福州大学与三聚环保等单位通过产学研深度融合,于2017年5月在禾友化工投资建立世界首套以煤为原料的万吨级“铁钌接力催化”氨合成工业装置。在此基础上,三聚环保、福州大学、禾友化工共同合作,对禾友化工原有传统铁基氨合成系统进行彻底改造,改造后的世界首套20万吨级以煤为原料的铁钌接力催化氨合成装置,于2019年7月一次性开车成功,至今已累计稳定运行6000小时以上,并于2020年4月通过了中国石油和化学工业联合会组织的72小时现场考核标定。标定结果显示:新装置本质安全性显著提高,吨氨综合能耗降低220元以上,经济和社会效益显著。
专家表示,若该技术推广成功,按改造全国一半合成氨产能测算,每年可节约550万吨标准煤,减少CO2、NOx、SO2等排放上千万吨,将产生巨大的经济和生态效益。
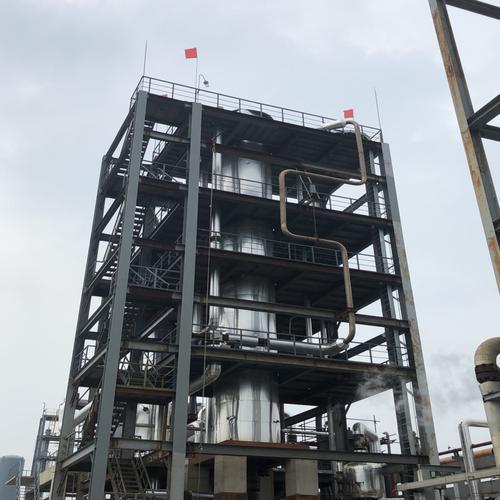
铁钌接力催化氨合成装置